The Science Behind Porosity: A Comprehensive Guide for Welders and Fabricators
Recognizing the complex devices behind porosity in welding is crucial for welders and makers aiming for remarkable craftsmanship. From the make-up of the base materials to the intricacies of the welding process itself, a multitude of variables conspire to either aggravate or ease the presence of porosity.
Recognizing Porosity in Welding
FIRST SENTENCE:
Evaluation of porosity in welding exposes essential understandings right into the stability and top quality of the weld joint. Porosity, characterized by the visibility of dental caries or spaces within the weld metal, is a typical concern in welding procedures. These voids, otherwise properly resolved, can jeopardize the architectural stability and mechanical buildings of the weld, causing potential failings in the completed product.
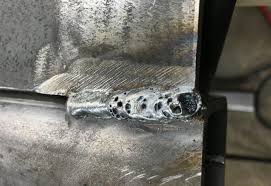
To spot and measure porosity, non-destructive screening methods such as ultrasonic screening or X-ray assessment are usually employed. These strategies permit the identification of internal problems without compromising the integrity of the weld. By analyzing the dimension, shape, and distribution of porosity within a weld, welders can make educated choices to improve their welding procedures and achieve sounder weld joints.

Elements Influencing Porosity Development
The event of porosity in welding is influenced by a myriad of factors, ranging from gas securing efficiency to the ins and outs of welding parameter settings. One crucial factor adding to porosity formation is insufficient gas shielding. When the protecting gas, generally argon or carbon dioxide, is not efficiently covering the weld swimming pool, climatic gases like oxygen and nitrogen can contaminate the liquified steel, resulting in porosity. Furthermore, the sanitation of the base materials plays a significant role. Pollutants such as corrosion, oil, or wetness can vaporize during welding, creating gas pockets within the weld. Welding specifications, consisting of voltage, present, take a trip speed, and electrode kind, additionally influence porosity development. Utilizing improper settings can generate excessive spatter or heat input, which consequently can cause porosity. Additionally, the welding technique employed, such as gas steel arc welding (GMAW) or secured steel arc welding (SMAW), can influence my site porosity formation due to variations in warm circulation and gas coverage. Recognizing and managing these variables are crucial for minimizing porosity in welding operations.
Impacts of Porosity on Weld Quality
The visibility of porosity additionally compromises the weld's resistance to corrosion, as the entraped air or gases within the spaces can respond with the surrounding setting, leading to degradation over time. Furthermore, porosity can hinder the weld's capability to stand up to stress or influence, further jeopardizing the general high quality and reliability of the welded structure. In essential applications such as aerospace, automobile, or architectural constructions, where safety and toughness are critical, the damaging impacts of porosity on weld high view it quality can have severe repercussions, stressing the significance of minimizing porosity via correct welding strategies and procedures.
Techniques to Lessen Porosity
Furthermore, Related Site utilizing the proper welding specifications, such as the correct voltage, current, and take a trip rate, is crucial in preventing porosity. Keeping a constant arc size and angle during welding likewise aids lower the chance of porosity.

Utilizing the suitable welding strategy, such as back-stepping or utilizing a weaving movement, can likewise aid disperse warm equally and decrease the possibilities of porosity development. By carrying out these strategies, welders can effectively minimize porosity and create top quality welded joints.
Advanced Solutions for Porosity Control
Carrying out cutting-edge modern technologies and ingenious techniques plays an essential duty in attaining exceptional control over porosity in welding procedures. One sophisticated option is making use of sophisticated gas combinations. Protecting gases like helium or a mixture of argon and hydrogen can assist lower porosity by supplying much better arc security and improved gas protection. Additionally, using advanced welding techniques such as pulsed MIG welding or customized ambience welding can likewise assist mitigate porosity issues.
An additional sophisticated service includes making use of advanced welding devices. Utilizing devices with built-in functions like waveform control and innovative power resources can enhance weld quality and decrease porosity dangers. In addition, the execution of automated welding systems with precise control over parameters can substantially decrease porosity issues.
Additionally, integrating sophisticated tracking and assessment innovations such as real-time X-ray imaging or automated ultrasonic testing can help in finding porosity early in the welding procedure, permitting instant restorative actions. Overall, integrating these innovative remedies can substantially boost porosity control and improve the general quality of welded parts.
Verdict
Finally, comprehending the science behind porosity in welding is important for welders and fabricators to generate high-grade welds. By recognizing the aspects influencing porosity development and carrying out methods to minimize it, welders can boost the general weld quality. Advanced remedies for porosity control can additionally enhance the welding procedure and make sure a strong and trusted weld. It is essential for welders to constantly enlighten themselves on porosity and carry out best techniques to accomplish optimal outcomes.