The Best Guide To Welding Inspection
Table of ContentsWelding Inspection Fundamentals ExplainedThe Welding Inspection IdeasWhat Does Welding Inspection Mean?9 Easy Facts About Welding Inspection ShownThe Ultimate Guide To Welding InspectionFacts About Welding Inspection RevealedThe Definitive Guide for Welding Inspection
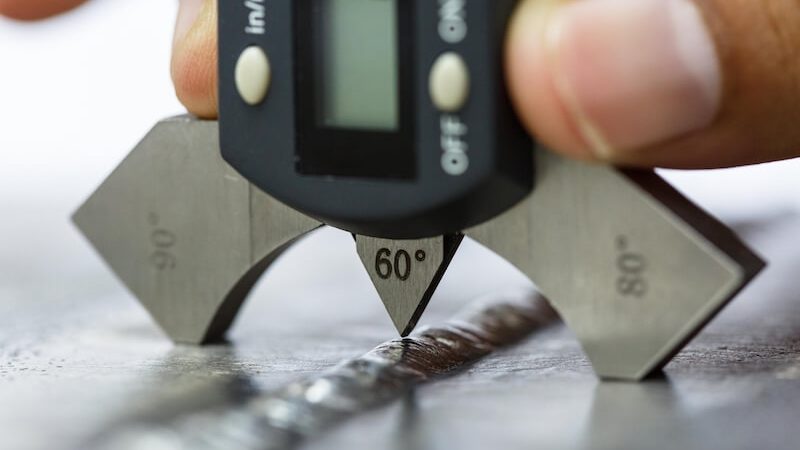
2 Elderly Welding Inspector levels with competence entailing ferrous as well as nonferrous products. Our technique to weld assessment as well as tracking It is essential to detect any kind of troubles with welds prior to they rise or not long after they take place so they can be fixed as swiftly as feasible. Component's weld inspectors review the quality of welds at every action of the construction procedure in the past, during, as well as after welding.
Customers have ranged from exclusive to public and large to little; the focus is always on maintaining a high criterion and compliance with the relevant code to make certain that your task has actually fulfilled every one of the essential demands be they code, regional, commercial or governmentally enforced laws and also or requirements.
The Only Guide to Welding Inspection
Swirl existing testing, In eddy existing testing, electromagnetic currents produce a magnetic field that interacts with the topic, producing localised swirl currents. Adjustments in stage and size show issues and can be gauged to quantify size, shape as well as area. High regularities are made use of to determine flaws at or near the surface area, while lower frequencies can penetrate deeper within the examination topic.

Various features of the weld may be assessed throughout a welding analysis, some concerning the weld measurements as well as others regarding making use of discontinuities of the weld. The dimension a weld might take is important since it can straight link to the weld's sturdiness and connected effectiveness, small welds may not stand up versus pressures used while in service.
Not known Factual Statements About Welding Inspection
These are acnes with or shut with the weld, that can or not relate to their dimension and/or place, block a weld from meeting its made performance. Generally, such stoppages, when are of unwanted dimension or area, are called welding problems as well as can also sometimes create very early weld failing though the decreasing of the weld's resilience or though producing stress and anxiety levels within the element of the weld. Welding Inspection.
The most standard purpose is to decide if the weld has an ideal as well as top-notch for the created program. To be able to access a weld's high quality, there should be some standard to which its attributes can be compared to. It is incorrect to try as well as access a weld's quality in the lack of some specific authorization requirements.

The Basic Principles Of Welding Inspection
This method is done in a workshop or field while the welding is being done. The things that are visually examined consist of the welder's certificate, slag elimination, joint preparation, climate condition, current utilized, and also problem of the electrode. 2- Magnetic Fragment Examining This test is used to find any surface or hardly subsurface issues in a weld.
Fragments of iron are then used to the magnetic field as well as if there are any kind of issues, the fragments of decision develop around the issue, which reveals where the defect is as well as why it happened. 3 Liquid-Penetrant Checking This test will detect defects in the surface of the weld like porosity and hairline cracks.
A programmer is after that used that will certainly reveal if any problems more info here show up. 4 Ultrasonic Evaluating This examination is accomplished by the use sound vibrations, which are after that transmitted via the bonded joint. The signals received on a glass screen will figure out if there are any kind of defects in the joint of the weld.
Some Known Factual Statements About Welding Inspection
5 Swirl Current Screening This test will certainly reveal exceptionally small cracks as well as is accomplished by the use a round coil that lugs alternating currents, which is put near the weld. The rotating currents will certainly develop a magnetic area, which will certainly interact with the weld as well as in turn, produce an eddy present.
The resulting indentation size is described as a solidity determining table. 8 Devastating Testing This test is a damaging examination that is completed by cutting the completed weld into pieces, this is per the code for origin bend, face bend, tensile test, as well as side bend. It is used to situate slag addition, porosity, as well as undercutting flaws in welds and is very effective.
This technique is done in a workshop or area while the welding is being done. The important things that are visually checked consist of the welder's certificate, slag elimination, joint preparation, weather, existing utilized, and also problem of the electrode. 2- Magnetic Fragment Evaluating This test is used to discover any kind of surface or hardly subsurface flaws in a weld.
All about Welding Inspection
Particles of iron are then applied to the electromagnetic field as you can try these out well as if there are any type of problems, the bits of iron will certainly accumulate around the problem, which reveals where the problem is and why it took place. 3 Liquid-Penetrant Examining This examination will detect defects in the surface of the weld like porosity and hairline fractures.
A programmer is after that used that will certainly reveal if any kind of issues are noticeable. 4 Ultrasonic Testing This test is accomplished by the usage of audio resonances, which are then transferred with the welded joint. The signals gotten on a glass display will establish if there are any type of defects in the joint of the weld.
5 Swirl Current Testing This examination will certainly reveal extremely small fractures as well as is completed by the use a circular coil that carries rotating currents, which is placed near the weld. The alternating currents will certainly produce an electromagnetic field, which will communicate with the weld and also subsequently, create an eddy present.
The Buzz on Welding Inspection
The resulting imprint size is referred to as a solidity gauging table. 8 Destructive Examining This test is a devastating examination that is accomplished by cutting the completed weld into items, this is per the code for origin bend, face bend, tensile examination, and also side bend. It is utilized to locate slag addition, porosity, as well as damaging issues in welds and also is extremely effective.